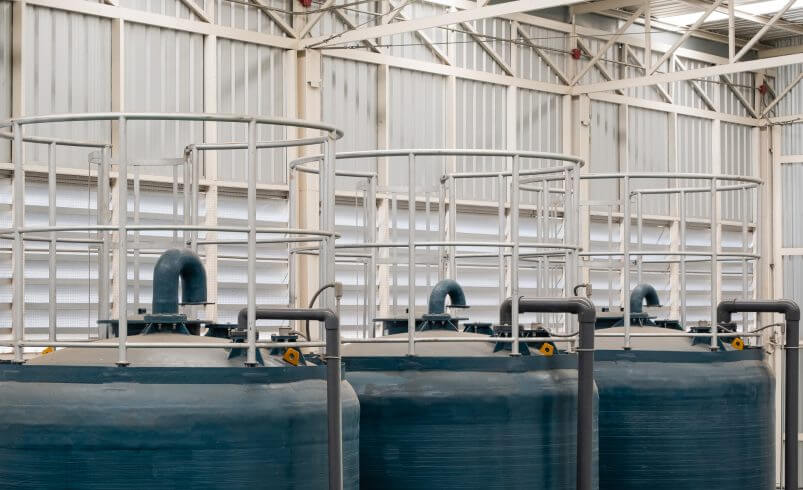
The Manufacturing Process of Fiberglass Water Tanks
Fiberglass and Dual-Laminate process equipment, tanks, scrubbers, etc are becoming increasingly popular due to their lightweight, corrosion-resistant, and low-maintenance nature.
These vessels are ideal for storing and processing a myriad of highly corrosive chemicals, waste waters & vapors, bleach, organic & inorganic chemicals, potable water, etc making them suitable for many industries and applications.
Let’s explore the step-by-step process of manufacturing fiberglass water tanks:
Stage 1: Design and Engineering
The first step in manufacturing a fiberglass water tank is the design and engineering phase. During this stage, engineers create a detailed 3D model of the tank using CAD (Computer-Aided Design) software.
They carefully consider the tank’s specifications, such as size, shape, and capacity, as well as any necessary reinforcements or fittings.
Once the design is finalized and proven to be in compliance with International industry standards, the engineers create a mold or pattern, which serves as a template for constructing the equipment.
Stage 2: Mold Preparation
Before the manufacturing process begins, the mold must be prepared. This involves cleaning and polishing the mold to ensure a smooth and defect-free surface.
Next, a gel coat is applied to the mold, providing a protective barrier between the mold and the fiberglass layers. The gel coat also gives the finished tank its glossy appearance and enhances its corrosion resistance.
In the case of Dual-Laminate equipment, a thermoplastic corrosion barrier is fabricated from sheets, welded and prepared to be bonded to the secondary FRP corrosion barrier and structure. A conductive layer is laminated between the thermoplastic and FRP to allow for spark test inspection during and after fabrication as well as during maintenance inspection once in service.
Stage 3: Layering of Fiberglass Materials
Once the mold is prepared, the layering of fiberglass materials begins.
This process involves applying alternating layers of resin and fiberglass reinforcement materials onto the mold surface.
The number of layers, the type of reinforcement material and process used depends on the specific equipment requirements and desired strength.
Stage 4: Curing and Consolidation
After the fiberglass layers have been applied, they need to cure and consolidate. This involves applying pressure to ensure that the fiberglass layers bond together and remove any trapped air or voids.
The resin then cures, hardening the fiberglass materials and creating a rigid, durable structure.
The curing process typically takes several hours.
Stage 5: Trimming and Finishing
Once the fiberglass materials have cured, the excess material is trimmed away, and any necessary fittings or reinforcements are added.
The equipment is then inspected for any defects or irregularities, which are repaired if needed. Finally, a thorough cleaning to remove any dust or debris completes the process.
Stage 6: Quality Control and Inspection
Before the finished equipment leaves the manufacturing facility, it undergoes a rigorous quality control inspection.
This includes visual inspections, as well as pressure and leak testing, to ensure all specifications and performance standards are met.
Once the equipment passes the quality control inspection, it is ready for shipping and installation.
FRP and Dual-Laminate equipment offer numerous advantages over traditional materials, making them an excellent choice for a variety of applications.
The manufacturing process, from design and engineering to quality control and inspection, ensures a high-quality, durable, and reliable for a long, trouble free service life.
By understanding the stages involved in the manufacturing process, you can appreciate the craftsmanship and precision that our company provides. Contact us today to get a free quote on your next project!