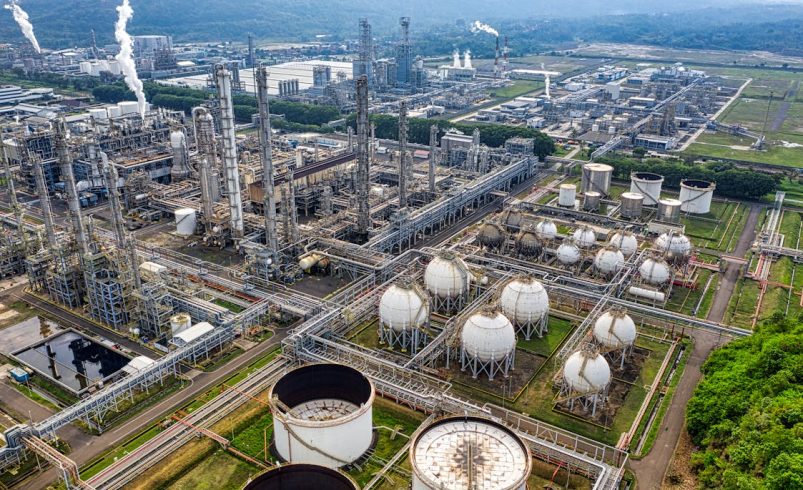
How to Use Industrial FRP Products to Engineer Durable Work Environments
Whether you’re managing a refinery, an oil and gas infrastructure, or any setting with corrosive chemicals, corrosion is the enemy of durability and safety. It’s a silent disruptor that, over time, weakens structural integrity, drives up costs, and can even create serious environmental problems. But here’s the thing: you don’t have to let it.
Fiberglass-reinforced plastic (FRP) offers a proactive, long-lasting solution that’s already transforming industrial corrosion control across sectors. Let’s look at how FRP storage tanks and other solutions can reinforce your infrastructure and, ultimately, simplify your life.
Industrial Corrosion Control
Staying on top of a corrosion management program isn’t just a nuisance—it’s an expensive problem. If you’ve ever had to pause operations to replace equipment corroded by acidic chemicals or saltwater, then you know all too well how much it disrupts operations and impacts the bottom line. FRP takes the edge off this risk. Its unique material properties provide high corrosion resistance, making it an ideal choice for industrial corrosion control in harsh environments.
Instead of worrying about an internal or external corrosion process weakening your pipelines, tanks, or ducting, FRP lets you focus on productivity.
How FRP Solves Major Corrosion Challenges in Industrial Settings
Imagine this: you’re running an industrial facility in a port city—maybe it’s a refinery, maybe it’s a chemical processing plant. Every day, your equipment faces some pretty tough customers: corrosive chemicals, extreme temperatures, even salt in the air. If you’ve ever watched steel go from solid to rusted-out in record time, you know exactly what we’re talking about. And it’s not just frustrating; it’s costly. You’re dealing with leaks, unplanned downtime, constant repairs… and let’s face it, it’s exhausting.
From acidic fumes to intense heat, FRP shrugs it off, protecting your operations from the wear and tear that metal just can’t handle. So instead of being caught in a never-ending loop of maintenance and downtime, you’re in control. You get equipment that lasts longer, needs fewer repairs, and keeps your production line moving like it should.
Here’s where it gets interesting: with FRP, it’s not just about avoiding corrosion. It’s about a whole new level of reliability. By switching vulnerable components—think storage tanks, pipelines, ducting—to FRP, you’re creating a work environment that’s built for the long haul. Those leaks and breakdowns? Practically gone. Suddenly, maintenance budgets stretch further, and production hits the high notes with far fewer interruptions.
FRP might not be the lowest-cost material at the outset, but it delivers unmatched value. Think about the long game—fewer replacements, a better lifespan for your infrastructure, and a lot less stress. It’s not just durable; it’s dependable. For industries where corrosion is always lurking, FRP offers a real solution that supports both productivity and peace of mind.
Corrosion Control in the Oil and Gas Industry
In the oil industry, equipment faces relentless exposure to the elements. This sector grapples with corrosive chemicals, high-pressure environments, and fluctuating temperatures that make standard materials prone to early failure. FRP is a different story. It’s not just a temporary fix—it’s a permanent upgrade for oil and gas infrastructures that extends equipment life, reduces maintenance, and supports a stronger bottom line.
Our FRP solutions provide corrosion resistance against everything from saltwater to chemical exposure. That means fewer repairs, fewer unplanned shutdowns, and a lot more peace of mind for your team. FRP is the powerhouse you need to control corrosion in your infrastructure.
Ready to see what FRP can do for you? Contact us today—a more durable, resilient operation is just a conversation away.