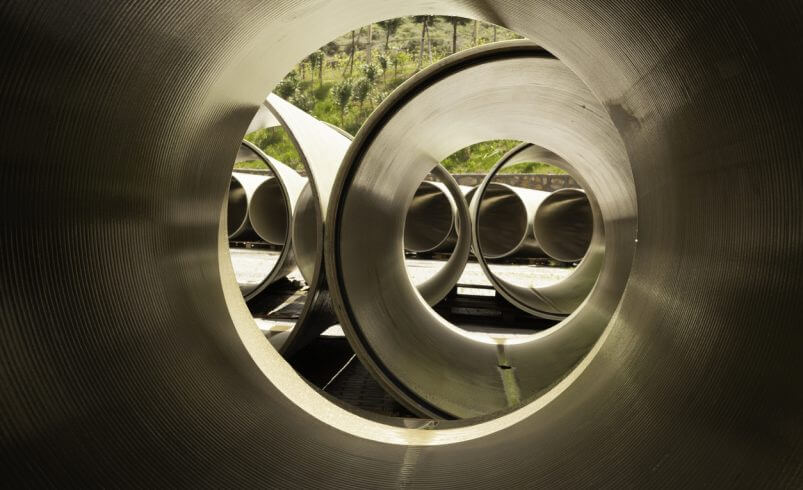
How Fiber-Reinforced Plastic is Made
Fiber-Reinforced Plastic (FRP) is a composite material. It has been gaining popularity in various industrial applications due to its corrosion resistance, lightweight, exceptional strength, durability, and versatility. It is made by combining a polymer matrix with reinforcing fibers in a multi-step manufacturing process.
Here, we’re going to explore the process of how FRP is made from preparing the fibers to curing the final product.
Step 1: Preparing the Fibers
The first step in making FRP is preparing the reinforcing fibers.
These fibers can be made of various materials such as fiberglass, carbon fiber, or aramid, depending on the specific application. The fibers come in the form of continuous strands, chopped strands or woven fabric. Each strand contains thousands of micro strands.
Fibers are typically coated with a sizing material that improves their bonding properties. The sizing also helps protect the fibers during the handling and manufacturing processes.
Step 2: Mixing the Resin
The next step in making FRP is mixing the polymer matrix with a hardening agent to create the resin.
The polymer matrix is typically made of polyester, vinyl ester, or epoxy resin. The hardening agent is usually a chemical catalyst that triggers a chemical reaction, causing the resin to harden and cure.
The resin can also be mixed with various additives such as fillers, pigments, and flame retardants. This is dependent on the desired properties of the final product.
Step 3: Layering the Fibers and Resin
The fibers and resin are then combined using various processes such as filament winding, contact molding or vacuum infusion.
The chopped strand mats and woven fabric or roving are arranged in the desired pattern.
The number of layers and the direction of the fibers are customized to achieve the desired thickness and physical properties.
Step 4: Curing the FRP
The final step in making FRP is curing the composite material.
The curing process is typically done in a temperature-controlled environment to ensure that the resin hardens and cures properly.
The temperature and curing time can be adjusted depending on the resin and the desired properties of the final product.
During the curing process, the resin undergoes a chemical reaction that causes it to harden and bond with the reinforcing fibers. This results in a strong and durable composite material that is ideal for use in various industrial applications.
At Troy Dualam Inc, we specialize in the fabrication and design of custom equipment in FRP and thermoplastic lined FRP, known as Dual-Laminates. Contact us today to learn more about how we can help you optimize your industrial processes and infrastructure with the advantages of FRP and Dual-Laminates.