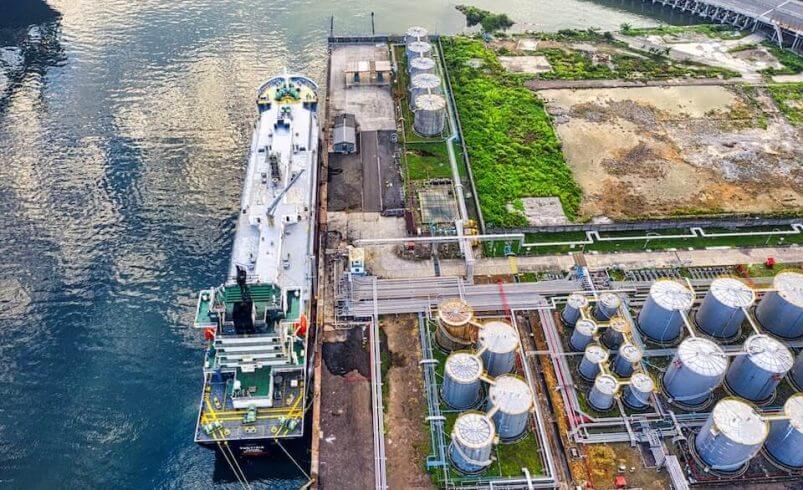
Réservoirs de stockage souterrains en PRF : Tout ce que vous devez savoir
According to market research from late 2024, the North American storage tank market is projected to grow steadily in the years ahead, with estimates putting the $24.34B(USD) market on pace to grow to over $44B(USD) by 2032. Why? The primary driver is expected to be the continued growth in energy demand, which will necessitate more safe storage solutions for oil and gas exploration and production.
Both underground and above-ground tanks have been around for decades, but not all industrial storage tanks are built the same. For years, steel was the go-to material. It did the job—until it didn’t. Corrosion, leaks, costly repairs, and environmental risks turned steel tanks into liabilities. That’s why fiberglass reinforced plastic (FRP) tanks have become the smarter choice. With industries needing better, longer-lasting storage for petroleum, chemicals, and wastewater, FRP has proven itself as the low-maintenance, high-performance solution for storing potentially hazardous materials and preventing environmental contamination.
What Makes FRP Tanks Different?
FRP tanks aren’t just an upgrade—they solve problems steel tanks can’t. Built from layers of fiberglass and specialized resins, these tanks won’t rust, corrode, or degrade over time. That means no protective coatings, no cathodic protection, and no surprise failures due to metal fatigue.
They’re also lightweight but incredibly strong, making installation easier without sacrificing durability. More importantly, they’re built to handle harsh chemicals, underground pressure, and changing environmental conditions—things that shorten the life of steel tanks.
Where Are FRP Tanks Used?
If a material is corrosion-resistant, long-lasting, and designed for underground conditions, it’s going to find a home in a lot of industries. FRP storage tanks are used for:
- Petroleum Storage – Gas stations, fuel depots, and aviation fuel storage.
- Chemical Processing – Handling caustic and acidic materials without risk of corrosion.
- Municipal Water Systems – Storing drinking water safely, with no risk of contamination.
- Industrial Wastewater – Containing hazardous byproducts without leaching into the soil.
These tanks are built for businesses that need long-term storage solutions without the risk of environmental damage or expensive repairs down the line.
Why FRP Tanks Outlast Steel
Steel has its place, but underground storage isn’t one of them. Left unprotected, it rusts. Even with coatings, it eventually breaks down, requiring costly maintenance and replacements. FRP avoids these issues entirely.
Corrosion-Proof – No rust, no need for internal linings or coatings.
Lightweight Yet Strong – Easier to install, without sacrificing structural integrity.
Designed to Last – Properly built FRP tanks have a service life of 30+ years.
Built for Secondary Containment – Double-wall designs keep leaks from becoming disasters.
For anyone storing hazardous substances, petroleum products, or chemically aggressive materials, FRP offers better long-term protection with fewer headaches.
How FRP Tanks Are Built
Not all FRP tanks are created equal. The right design depends on:
- What’s being stored – Fuels, chemicals, and potable water each require different resin systems.
- Soil conditions – Tanks must withstand underground pressure without risk of structural failure.
- Regulatory compliance – Environmental regulations dictate leak prevention and spill containment.
A well-built FRP tank will have:
- Internal Linings that protect against chemical attack and extend service life.
- Secondary Containment to prevent leaks from reaching surrounding soil.
- Leak Detection Systems for added environmental protection.
Troy Dualam designs custom FRP tanks that meet or exceed all industry and environmental standards. That means a tank that does its job—and keeps doing it for decades.
Installation: What You Need to Know
Even the best underground tanks won’t perform if it’s installed poorly. A proper installation follows a clear process:
- Site Preparation – Soil is tested and compacted to provide a stable foundation.
- Tank Placement – The FRP tank is positioned, anchored, and secured.
- Connections & Monitoring Systems – Leak detection and monitoring equipment are integrated.
- Backfilling & Final Inspection – The tank is enclosed with protective material, and a final compliance check is performed.
Get this process right, and an FRP underground storage tank will provide decades of trouble-free service. Cut corners, and problems will show up sooner than expected. That’s why experienced professionals should always handle the installation.
Troy Dualam: FRP Tanks Built to Perform
At Troy Dualam, we don’t just manufacture tanks—we build solutions that last. With decades of experience in FRP and Dualam composite manufacturing, we understand what it takes to engineer storage tanks that resist corrosion, meet environmental regulations, and hold up in real-world conditions.
Every tank we build is designed for long-term performance, whether it’s for fuel storage, chemical containment, or municipal water systems. Our team also provides 24/7 emergency support, custom fabrication, and on-site installation guidance to make sure your tank delivers exactly what you need.If you’re looking for a reliable, cost-effective FRP underground storage tank, let’s talk. Contact us today to discuss your project.